EnergyX utvikler ny spyledyse ved hjelp av 3D-laserprinting
I stedet for å måtte skru sammen flere deler fikk bedriften alt i en del.
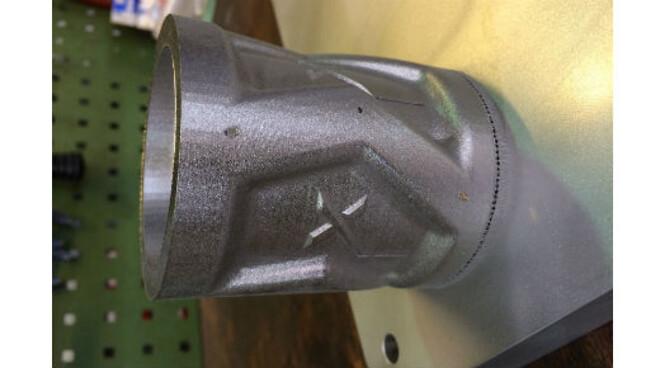
De 3D-printede spyledyser skal brukes i utleieverktøy. Bedriften har 10 stk. vaskeverktøy av denne typen i forskjellige størrelser på lager.
- Vi styrker vår engineering-avdeling, så vi kan levere alt fra skisse over design til ferdig testet produkt, sier Jan Kåre Bredal.
3D-printet spyledyse
En av bedriftens tradisjonelle servicer er å leie ut vaskeverktøy, som brukes for å spyle vekk avsetninger i oljebrønner.
EnergyX har i det siste drevet med videreutvikling for å finne nye bruksmåter for dette verktøyet. Blant annet har man holdt på med å utvikle en roterende spyledyse for høytrykksvasking, med geometrier som det ikke var mulig å produsere med tradisjonell CNC-maskinering.
- Vi hadde laget en design med en spyledyse som vi gjerne ville lage men dysen hadde en innvendig geometri, som vi ikke klarte å maskinere i et CNC-verktøy, og da kom opp ideen om å 3d-printe det, sier Jan Kåre Bredal.
Nylig inngikk EnergyX derfor en avtale med Promet, som er en av pionerene i Norge innen 3D-printing.
- Vi sendte en 3D-modell som viste dem hvordan vi ville ha delen, og Promet vendte tilbake med forslag til noen forandringer, som ville gjøre dysen enklere å printe. Vi gikk noen runder og Promet hadde veldig bra innspill til hvordan man kunne gjøre det billigere, forteller Jan Kåre Bredal.
Deretter har Promet produsert spyledysen i full størrelse i inconel 718, som er mye brukt i nedihulls-bransjen. Metallet som er syrefast har meget gode mekaniske egenskaper og tåler surt miljø, forklarer Jan Kåre Bredal, som legger til at det er et kostbart materiale.
Han kan dog trøste seg med at det ved laserprinting ikke går med mer metallpulver enn høyst nødvendig – da det nesten ikke er noen svinn i produksjonen.
Godt fornøyde med resultatet
Produksjonen har ifølge Jan Kåre Bredal gått veldig greit.
- Vi er veldig godt fornøyde med den ferdige dysen, og vi har til og med fått vår egen logo inngravert i produktet, sier han.
- Vi holder fortsatt på med testing, men dysen fungerer som forventet. Vi har ikke hatt den med på jobb enda bortsett fra som backup-verktøy, sier han og legger til at den 3D-printede spyledysen etter planen skal tas i bruk innen utgangen av året.
Ifølge prosjektlederen er både toleransen og finishen på produktet mer enn godkjent med tanke på at det er printet i inconel.
- Vi spente det opp i en CNC maskin, og der maskinerte vi noen pasninger med fin toleranse og det fungerte bra.
- Vi har ingen erfaringer som tilsier at dette ikke skulle være like sterkt som hvis det var maskinert ut av en bolt, sier Bredal.
- Gjerne igjen
Med tanke på økonomien kom man ifølge prosjektlederen greit ut av prosjektet.
- Det er jo dyrt å få laget i 3D, men omtrent som forventet. Hvis vi får ut dette produktet er det snakk om å få laget andre størrelser av det samme produktet, sier han, og legger til at han regner med at EnergyX fremover vil benytte seg av 3D-printing på prototyper og deler, som bedriften ikke greier å maskinere selv.